基于寿命周期的航空装备定费用设计与控制
2024-01-01王江三高伟席林军
摘 要 基于面向寿命周期的定费用设计与控制既不是追求极限的技术性能指标,也不是追求最小的寿命周期费用,而是将目标成本控制起始点前移到需求生成阶段,强调在经济可承受指标范围内实现技术指标和寿命周期费用的最佳平衡,并基于寿命周期成本初始基线进行严格管控。本文基于某航空装备典型部件尾翼,通过价值工程、寿命周期成本预测开展了寿命周期定费用设计工作,并对寿命周期的定费用控制进行了详细阐述,文中采用的逻辑、方法可为航空装备成本工程师所借鉴参考。
关键词 航空装备;定费用设计;寿命周期;目标成本
DOI: 10.19840/j.cnki.FA.2024.05.010
随着科学技术的进步和装备技术指标要求的提高,航空装备寿命周期费用也在大幅上涨[1]。寿命周期费用看似是其各个阶段费用相加之和,但是总体设计方案一旦确定,寿命周期费用的65%左右也就大体确定,待详细设计和鉴定工作完成后,寿命周期费的85%便已经确定[2]。为确保以国家经济可承受得起的价格采购具备技术优势的航空装备,总体单位必须基于设计源头开展面向寿命周期的定费用设计工作。
传统的定费用设计是将科研费、目标价格和使用保障费等费用指标,作为与性能、尺寸、重量、可靠性、维修性等技术指标同等重要的一种设计原则和思想,技术指标和寿命周期内各项费用指标均要达到既定的目标[3-5]。基于面向寿命周期的定费用设计既不是追求极限的技术性能指标,也不是追求最小的寿命周期费用,而是将目标成本控制起始点前移到需求生成阶段,强调在经济可承受指标范围内实现航空装备体系能力、寿命周期费用和可支配资源三者之间的最佳平衡。
一、面向寿命周期的定费用设计
面向寿命周期的定费用设计,就是基于经济可承受性进行寿命周期内成本控制。寿命周期目标成本应由技术、管理、经济、质量管理等多部门基于技术优势识别、国民经济水平及预期科学分析与决策得出,同时在研制过程中对目标成本严格控制、连续不断地审核、迭代,使之寿命周期内成本可控[6]。
(一)经济可承受性分析
航空装备经济可承受性分析是指从装备效能、战技指标与经济指标结合的角度进行可行性分析,预测航空装备寿命周期成本,以及研制、采购、使用保障等各阶段所需经费投入,分析产品是否满足装备开支的长期投资,以此来平衡装备寿命周期成本与性能等技术指标。经济可承受分析主要有计划年度投资法和单位成本法[7]。
1. 计划年度投资法需全面考虑航空装备研制进度、成本费用、技术指标、人力投入等各方面要素,从航空装备能力聚类的更高角度,在较长周期跨度内,对航空装备经济可承受性进行评估。
2. 单位成本法是对具体项目进行经济可承受性分析。高度集成的系统、子系统成本费用十分昂贵,需评估本项目总体经济可承受性和子系统的经济可承受性。
面向寿命周期的定费用设计经济可承受性分析主要针对某具体项目及其附属高度集成/高价值的系统进行经济可承受分析[8]。经济可承受分析构建的评价指标需具备客观性、独立性、完备性、简洁性和可度量性的特点,通过分级指标的构建、分解、计算完成装备经济可承受分析工作。
(二)寿命周期目标成本
寿命周期成本包括研究与发展成本(论证、研制、试验和鉴定费)、投资成本(生产采购费用)、使用与保障成本和处理成本。寿命周期成本测算流程为:明确假设和约束条件。主要包括基准年和货币单位、通货膨胀率、部署方案、使用和保障方案、维修要求、使用年限、有关采办里程碑的限制和范围、采办策略、生产数量、研制和样机数量、进度信息、技术假设和要研发的新技术等;编制计划项目说明书。主要包括航空装备项目的关键技术、计划、使用以及综合数据资料;编制装备工作分解结构。依据GJB 2116A-2015《武器装备研制项目工作分解结构》建立系统性、完整性和层级适度的航空装备工作分解结构(Work Breakdown Structure, WBS);选择成本估算方法(成本估算方法主要有工程估算法、参数估算法和类比法);收集数据。主要收集研制、生产成本数据和使用与保障成本数据;编制寿命周期成本测算报告。
寿命周期目标成本估算和审查完成后,总体单位必须制定初始成本基线,并按成本基线对其寿命周期成本进行严格管控。各里程碑决策点时,实际成本与成本基线出现较大偏离时按规定审批程序进行报批。
(三)定费用设计权衡
定费用设计权衡主要指技术指标与目标成本的权衡,主要工作包括:将目标成本引入日常设计工作,开展技术经济效果权衡,利用成本和性能之间的映射关系,把成本作为一个主要设计参数,来评定设计工作的有效性;设计工程师要与成本工程师充分沟通协调,考虑设计对后续阶段成本的影响,做好预防性设计,使航空装备经济可承受;以客户的功能要求、技术性能指标和作战使用要求为出发点,研究功能性能、使用要求与成本之间的关系,全系统多层级进行效能—费用综合权衡[9];在整机级、系统级、分系统级、产品设备级、组件部件级开展价值工程分析,确定功能性能,寻求降低获得必要功能所需费用的备选方案,在不损害所要求的质量、可靠性的前提下,剔除冗余功能,发现和消除不必要的费用;可充分借鉴历史型号的经验教训,吸收以往型号的优点和亮点,降低寿命周期成本。
二、尾翼定费用设计实例
某航空装备尾翼定费用设计主要从价值工程分析和寿命周期成本预测分析两个维度开展定费用设计工作。
(一)价值工程分析
某航空装备尾翼针对金属与复合材料两种构型方案开展权衡对比分析。假设尾翼结构采用相同的外形、载荷、结构布置、传力路径、金属材料肋与接头结构、载荷工况进行计算,分别满足强度应力或应变水平控制要求、有相当的刚度要求,所不同的是尾翼的梁、壁板分别采用金属与复合材料结构。
1. 壁板重量权衡对比
复合材料壁板拉伸应变取值4000με,压缩应变取值3500με,剪切应变取值5000με。金属壁板控制应力的设计要求是受压载荷为主的翼面应力水平不大于345MPa,受拉为主翼面载荷应力水平不大于310MPa。
在进行重量估算时,假设长桁占整个壁板横截面积35%,复合材料蒙皮模量取值60GPa,复合材料长桁模量取值80GPa,则拉伸载荷为主的应力水平取值为4000με×60Gpa×0.65+ 4000με×80Gpa×0.35=268Mpa,压缩载荷为主的应力水平取值为3500με×60Gpa×0.65+ 3500με×80Gpa×0.35=234.5Mpa。复合材料加筋壁板密度按1.6g/cm3估算,由此可以得到复合材料加筋壁板受拉载荷为主的壁板单位密度应力水平为268÷1.6=167.5;受压载荷为主的壁板单位密度应力水平为234.5÷1.6=146.6。金属壁板受拉载荷为主的壁板单位密度应力水平为310÷2.7=114.8;受压载荷为主的壁板单位密度应力水平为345÷2.7=127.8。受拉壁板减重效率为(167.5-114.8)÷167.5×100%=31.4%;受压壁板减重效率为(146.6-127.8)÷146.6×100%= 12.8%。通过重量权衡对比分析,尾翼壁板结构采用复合材料结构优势明显。具体差异见表1。

2. 翼梁重量权衡对比
翼梁主要由梁缘条和腹板构成,梁缘条主要承受尾翼弯曲载荷转化为拉、压载荷,腹板主要承受剪切载荷。采用复合材料梁结构可以通过铺层设计,使上下缘条拉伸模量、腹板剪切模量较大,从而使翼梁结构效率最大化、降低结构重量。结合壁板重量权衡对比章节结论,翼梁采用复合材料结构重量收益明显,同时可以有效解决尾翼展向翼梁与壁板的热膨胀差异性问题。
3. 成本权衡对比
复合材料结构件的成本主要体现在材料、制造(设备、模具工装、制造工艺)、后加工、无损检测以及装配等方面。在不计入模具成本时,按目前国际材料价格估算,复合材料整体壁板及梁的制造成本(含无损检测成本)为0.74万元/kg。每架机尾翼复合材料结构件重量共200kg,制造费用约为148万元。大型复合材料制件需要的INVA合金模具造价较高,成本约为11万元/平方米,完成一架尾翼整体壁板及两根翼梁所需模具面积约为38平方米。模具投入418万元,考虑模具属于一次性投入,按50次(保守估计,一般可用100次以上)批生产进行分摊,成本仅增加8.38万元/架。考虑模具费用后,每架机尾翼复合材料结构件制造成本为156.36万元。
金属尾翼采用整体加筋壁板,梁也是整体机加件。壁板材料为2024厚板(110元/kg)机加和7150厚板(150元/kg)机加,前后梁为7050厚板(150元/kg)机加。金属尾翼方案结构重量约为235公斤[按复合材料减重15%估算(200kg/(1-15%)],2024厚板137kg、7050厚板40kg、7150厚板58kg,材料利用率按5%、制造费用按等于材料成本估算,金属尾翼制造成本约为:[(137÷0.05×110)+(40÷0.05×150)+(58÷0.05×150)]×2÷10000= 119.08万元。
通过成本对比分析,复合材料尾翼较金属尾翼生产成本增加约37.28万元/架,再考虑装配因素(构件整体化程度高、装配工时减少、标准件数量减少),增加值会有所下降。空客公司数据表明,在生产100架民用航空飞机的条件下,每减轻1kg重量允许进行8000马克(1984年经济条件)的投资,换算成人民币约8万~12万元(购买力)。复合材料尾翼较金属尾翼减重约35kg,则相应可以增加280万~420万元的投资。综上,复合材料尾翼成本存在一定优势。具体差异见表2。
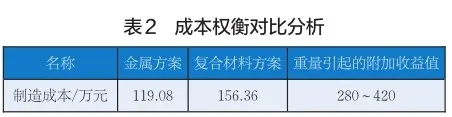
(二)寿命周期成本预测分析
研究与发展阶段设计方案直接决定寿命周期成本,投资成本和使用与保障成本是寿命周期成本的主要构成。因此,某航空装备尾翼主要对其投资成本和使用与保障成本进行了预测分析。
1. 投资成本
投资成本预测方法主要有工程法、类比法和参数法三种。工程法是一种自下而上的方法,估算所需的基础数据量大,过程复杂,周期长,不适合方案早期的费用评估;参数法是根据已有同类型飞机研制费用的大量历史统计数据,通过相关分析选择一组对费用影响较大的物理和性能参数,运用回归分析方法建立以这些参数为自变量的费用估算关系式,以此来完成投资成本估算;类比法一般应用于新型航空装备概念设计阶段。
某航空装备尾翼投资成本基于类比法进行预测分析。经数据搜集、统计民用航空器成本密度见表3,成本密度平均值为66.49万美元/吨。
某航空装备最大起飞重量为20.5吨,投资成本20.5×66.49=1363.04万美元。经统计尾翼重量约占机体结构重量比例的6%,结合市场竞争力需求,某航空装备尾翼投资成本不应超过81.78万美元/架进行控制。
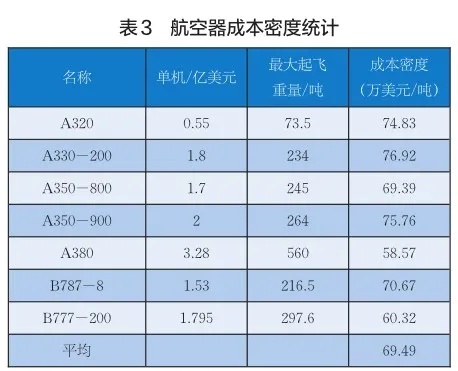
2. 使用与保障成本
本文基于Liebeck[10]模型对某航空装备尾翼使用与保障成本中维修成本进行预测。某航空装备尾翼维修成本主要包括机体维修劳务成本和机体维修材料成本两部分。
(1)机体维修劳务成本
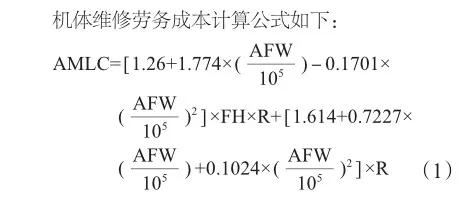
其中: AMLC为机体维修劳务成本,单位美元/航段;AFW 为不含发动机的机体重量,单位磅;FH为每航段飞行小时数,取轮档小时减去地面机动时间(通常约0.25小时);R为维修劳务费率,单位美元/小时,Liebeck模型中取值为25美元/小时,考虑经济环境及年代不同等客观因素取值28美元/小时。
经计算,AMLC为28.67万美元/架。
(2)机体维修材料成本

其中:AMMC为机体维修材料成本,单位美元/航段;FCPI 为消费者价格指数修正系数,基于CPI上涨情况,取值1.47。
经计算,AMMC值为14.96万美元/架。
(3)维修成本
经计算,某航空装备尾翼维修成本合计43.63万美元/架。
三、面向寿命周期的定费用控制
影响寿命周期成本的主要为投资成本和使用与保障成本。投资成本主要由材料成本和制造成本构成;使用与保障成本主要受机体重量影响。材料选择、制造工艺和机体重量均在研究与发展阶段确定,因此,面向寿命周期的定费用控制主要是研究与发展阶段材料体系的选择、制造工艺的确定和机体重量的优化。
(一)材料体系选择
材料体系选择控制主要为:重视新材料及相关工艺的成本控制,在满足设计及使用要求的前提下,优先选用综合成本低的新材料及加工工艺方法;重视材料的工艺性、工业化生产、批量供应能力和质量稳定性;随着生产批量的增加,在满足技术要求的前提下,细化专业化生产分工,进一步提高材料利用率,从而提高材料的制造成熟度,降低产品报废率;尽可能减少或压缩材料牌号、品种、规格,减少材料、工艺的复杂度,在便于材料采购的前提下,改善因原材料用量少而引起的采购成本提高,最终达到降低原材料采购成本的目的;优化合并入厂复验项目,降低入厂复验费用。
某航空装备尾翼材料的选用坚持性能优先、市场成熟和尽可能减少/压缩材料牌号的原则,复合材料主要选用了市场成熟度高、用量规模大的T800级中等模量高强度碳纤维预浸料,金属材料主要选用了7050-T7451预拉伸板铝合金。
(二)制造工艺的确定
复合材料制造工艺主要有手工铺贴、自动铺带技术(ATL)和自动纤维铺放技术(AFP)三种工艺。工业部门统计结果表明:手工铺叠复合材料效率为3磅/h,自动化技术能达到15~30磅/ h;手工铺叠复合材料废料量为15%~20%,而自动化技术可以减少到5%左右。因此,复合材料制件可通过自动铺带技术(ATL)和自动纤维铺放技术(AFP)来提高制造效率、材料利用率,从而降低生产成本。
为有效降低某航空装备尾翼复合材料制件制造工时,其大尺寸复合材料制件采用自动铺带技术(ATL)来提高铺贴效率、材料利用率进行费用控制。
(三)机体重量优化
某航空装备尾翼首先以盒段变量为设计参数,在PATRAN中建立盒段参数化模型并进行强度和稳定性求解,形成ses文件;其次应用MATLAB编制遗传算法优化程序,根据盒段设计变量设定优化变量;然后将遗传算法产生的初始变量值赋值给PATRAN中的ses文件参数,自动建立有限元模型并进行稳定性求解;最后将求解结果传递到遗传算法中进行变量的适应度分析,根据适应度分析结果进行选择、交叉和变异等遗传算法的操作后,再次进行参数化建模和求解等循环工作,直至循环到达设定的遗传代数,得到其最优结果。
某航空装备尾翼通过优化设计确保应变分布合理、结构轻质高效,得到较优结构重量。
四、结束语
随着武器装备改革不断向前推进,研究与发展阶段基于面向寿命周期的航空装备定费用设计与控制工作显得尤为重要。研究与发展阶段只有从设计思想、规定、准则、流程和方法上不断完善定费用设计能力,航空装备寿命周期的投资成本(生产采购费用)、使用与保障成本和处理成本才能得到有效控制,才能满足未来的新型航空装备军事优势、技术领先和国民经济可承受的多维度要求。 AFA
参考文献
[1] 赵国铭,刘祥静.美国定费用设计方法的应用研究[J].企业与管理,2012:92-96.
[2] 飞机设计手册总编委会.飞机设计手册第22册:技术经济设计[M].北京:航空工业出版社,2001.
[3] 王泽宇.航空装备研制中的限成本设计[J].航空科学技术,2017, 28(12): 61-64.
[4] 刘俊国、李毅.经济可承受性约束下的目标成本管控[J].航空财会,2023(3): 28-31.
[5] 刘畅,张海军,霍玥玥,等.复合材料加筋壁板低成本控制研究[J].航空财会,2024(2): 44-48.
[6] 刘晓东.装备寿命周期费用分析与控制[M].北京:国防工业出版社,2008.
[7] 张玉华.美军装备价格管理研究[M].北京:国防工业出版社,2016.
[8] 钱斐斐,宋杨.面向全寿命周期成本的民用飞机定费用设计(DTLCC)方法研究[J].价值工程,2017,36(22):3-6.
[9] 邓修权,张江侠,孙需要,等.考虑经济可承受性的直升机总体方案评估[J].航空科学技术,2018,29 (5):55-65.
[10] Kaufmann,Markus.Cost/Weight Opti‐mization of Aircraft Structures[D]. Sweden:School of Engineering Sciences, 2008.
(编辑:张春红)