智慧桥梁预制构件厂建设实践
2024-01-01陆怡罗金标严宗雪赖富才李海翔卢明子曾锋林敬辉孙一方
[摘 要]在国家大力推进智能建造与建筑工业化协同发展的大背景下,建筑行业预制构件生产转型升级迫在眉睫。广州公路工程集团有限公司立足粤港澳大湾区核心广州南沙,依托南中高速公路项目,利用云计算、大数据、物联网、人工智能等新一代数字技术,建成迄今为止国内领先、规模最大的智慧桥梁预制构件厂,并引入和改进环形生产线, 搭建起基于BIM技术和数据驱动的智慧构件厂管理系统,实现了预制构件生产智能化及全过程数字化管理,为桥梁全预制装配施工提供了可借鉴的样本。
[关键词]建筑工业化;智能建造;预制构件生产
一、公司简介
广州公路工程集团(简称“集团”)成立于1984年,原隶属于广州市公路管理局,2009年“大部制”改革时成建制移交广州交通投资集团有限公司。2021年6月,集团圆满完成公司制改革。
经过40年的发展,集团目前已成为集路桥施工、市政工程、道路养护、试验检测、设计咨询、预制装配等于一体的交通基础设施综合服务商,是广东省路桥建设龙头企业。
作为广东省公路施工建设的排头兵和主力军,广州公路工程集团现有注册资本5.6亿元,具有国家公路工程施工总承包特级资质、公路行业甲级设计资质、市政公用工程施工总承包一级资质,桥梁工程、路基工程、路面工程专业承包一级资质、养护工程全类从业资质及公路工程综合乙级试验检测资质,主要从事各等级的公路工程施工总承包、工程总承包,市政公用工程施工总承包,公路市政养护保洁和工程试验检测业务,是目前广东省唯一一家拥有公路工程施工总承包特级资质的地方国有企业,同时也是广州市应急抢险战备的重要力量。
集团自成立以来,已参加100余条国家、省市重点高速公路建设项目和200余条国道、省道的建设,多次斩获中国土木工程詹天佑奖、国家优质工程金奖、李春奖及全国优质工程金奖等公路行业最高级质量奖项,为构建现代化国家综合立体交通网奉献了强有力的筑路先锋力量。
截至目前,集团已连续11年荣获广东省公路施工企业信用评价最高等级AA企业,连续13年荣获广东省“守合同、重信用”企业,并连续3年获国家交通运输部认定公路施工企业全国综合信用评价最高等级AA级。集团还相继获评中国建筑行业AAA级信用企业、AAA级诚信企业、“十二五”高速公路建设优秀单位、全国公路建设施工企业重点工程劳动竞赛优胜单位、广东省法治文化建设示范企业、广州市思想政治工作先进单位、广州市建筑业优秀企业、广州市安全文化示范企业等,并获得全国工人先锋号、广东省五一劳动奖状、广东省青年文明号、广州市创先争优先进基层党组织、广州市先进集体、广州市国资系统先进基层党组织等荣誉。
二、实施背景
(一)基础设施建设绿色发展的需要
党的二十大报告提出,“优化基础设施布局、结构、功能和系统集成,构建现代化基础设施体系”“推动绿色发展,促进人与自然和谐共生”。这为新时代推进基础设施建设绿色发展指明了方向。
作为基础设施建设重要组成部分,交通基础设施建设必须以云计算、大数据、物联网、人工智能等新一代数字技术为支撑,改变传统粗放式建造模式,加快绿色、低碳、智能发展。其中,推动装配式、工业化建造是重要突破口。
对此,国家专门出台一系列政策,大力推动智能建造与建筑工业化协同发展。珠三角成为重点推进地区。广东省政府、广州市政府也先后出台相关政策,全面推动预制装配式建筑发展。
近年来,随着粤港澳大湾区等一大批国家发展战略布局的重点工程项目在珠三角落地,广东省的基础设施建设与改造也进入新一轮高速发展期。如何在交通基础设施改造过程中实现预制构件(尤其是装配式桥梁)快速、环保、绿色发展,面临着巨大挑战。
作为珠三角的龙头城市,广州市城市空间的承载限度现已变得越来越小,基础设施建设已不像以前那样拥有相对开放、宽敞的施工场地,原有的现浇施工法无法满足施工空间和交通保畅的要求。采用全装配式施工方法,成为城市基础设施建设的必然选择。
(二)预制构件生产转型升级的需要
全装配式施工主要依托预制构件厂来展开。当前,虽然传统预制构件厂仍然是桥梁构件施工的主要场所,但是随着经济社会和行业的发展,其弊端日益凸显。
传统预制构件厂通常都是随着项目建设进展进行建设或拆除,造成了极大的资源浪费。特别是传统预制构件厂存在空间需求高、生产工艺及生产设备落后、自动化程度较低、台座利用效率低、制造周期长等缺点。主要体现在以下几个方面:
一是传统预制构件厂需要较大的预制台座和存放台座空间,这对于城市有限的土地资源来说是一个巨大的挑战。
二是传统预制构件厂采用的是固定台座,预制构件生产占用时间长,台座周转效率低。
三是传统预制构件厂一般采用拼装式钢模板,构件外观质量和精度难以控制,同时采用吊装料斗进行布料,容易造成混凝土离析且安全隐患较高。
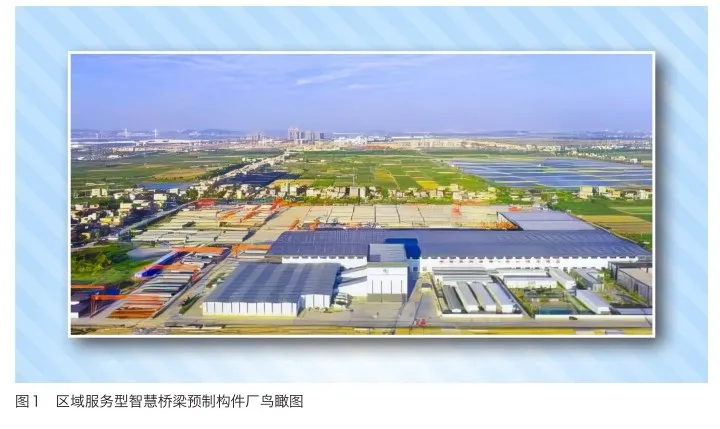
四是传统预制构件厂各道工序需要大量的工人,由于品质工程创建需要及人工成本逐渐高涨,由自动化设备代替人工生产大势所趋。
在“双碳”战略实施、国家大力推行标准化生产和工业化建造的背景下,高资源消耗、高人工成本投入、生产效率低的传统桥梁预制构件生产模式必然会被淘汰。因此,进行预制构件生产数字化、智能化转型升级迫在眉睫。
三、主要做法
2021年初,广州公路工程集团依托南中高速公路项目,建成了迄今国内领先、规模最大、占地面积为350亩的智慧桥梁预制构件厂。智慧桥梁预制构件厂主要为南中高速公路项目广州段提供7468榀预制构件生产服务(混凝土总量28万立方米),其中包括7379榀预制小箱梁和89榀预制T梁,生产工期为30个月。(如图1所示)
智慧桥梁预制构件厂位于广州市南沙区万顷沙镇,依据预制构件生产工序流程合理布局,分为办公研发区、生活区、混凝土加工中心、预制构件环形生产车间、预制构件常规生产区、小型预制构件生产区、试验检测中心、构件存放区共八个功能分区。当前,预制构件年设计产能为15万立方米,日设计产能为22榀。其中,预制构件环形生产车间(8条环形生产线)日设计产能为8榀,预制构件常规生产区布置固定台座130个,日产能为14榀,可满足20- 40米各种类型的预制小箱梁以及40- 50米各种类型的预制T梁施工。
为改变传统预制构件生产线生产工艺、生产设备落后、自动化程度较低、生产效率低、占地面积大、制造周期长、台座利用率低等问题,智慧桥梁预制构件厂按照智能化、数字化要求,引入并改进了“环形生产线”,建立了基于BIM技术和数据驱动的智慧预制构件厂管理系统,实现了桥梁预制构件生产智能化及全过程数字化管理。(如图2所示)
智慧桥梁预制构件厂的生产模式可逐步拓展到装配式桥梁其他构件生产中,如预制立柱、预制盖梁、预制防撞护栏等,可为桥梁全预制装配施工和装配式桥梁行业发展提供借鉴参考。
(一)“永临结合”建设模式
智慧桥梁预制构件厂采用“永临结合”方式高标准建设,地块租期为12年,用地许可结合持续承接项目进行续期,一次建设即可长期服务周边项目建设。另外,通过区域服务型智慧预制构件厂的拓展推广,可将构件生产服务辐射至广州市其他城区及东莞、中山、佛山等地,覆盖以智慧预制构件厂为中心、周边80千米为半径的区域,可以省去临时构件预制场地重复建设,减少对土地的破坏和占用,提高土地利用率。目前,预制构件厂已为中山市金字山互通立交工程、中山市南外环道路改造工程、广州市七星岗互通立交工程提供过预制构件生产服务。
同时,通过引进环形生产工艺,将传统的固定台座转化为移动台座,将各道施工工序集成到流水化的生产线上,可大大减少台座占地面积,实现智慧预制构件厂总体用地节约。
(二)设备自动化升级改造
在桥梁大型构件生产过程中,工装设备发挥着关键性作用。目前,预制构件环形生产技术尚在发展完善阶段,环形生产线各工装设备性能及相互之间的使用配合还不成熟,还有诸多问题需要解决。
通过对环形生产线进行升级改造,有效解决如生产线存在诸如鱼雷罐输送效率低、作业时布料机与工人相互干扰、生产线空间布置不合理等方面的问题。
1.混凝土环形运输系统及桁架布料系统
现阶段,传统预制构件厂在日常生产中采用混凝土运输车配合简易料斗进行运输及布料。该作业方式效率低、混凝土品质易波动、作业环境差、安全风险大。
部分预制构件厂对鱼雷罐运输系统及桁架布料系统进行初期应用,尚有一些缺陷亟须改善。一方面,当前使用的单通道鱼雷罐混凝土运输系统无法形成循环回路,且鱼雷罐从拌合站到浇筑区需要爬坡,运输效率低,设备磨损大;另一方面,布料系统布料时不能升降,因布料高度过大引起的混凝土离析问题、工人作业空间与布料机桁架相互干扰问题无法同时得到解决。
智慧预制构件厂以现代化、信息化、智能化、环保化的建厂理念为出发点,自行规划设计出一套混凝土环形运输系统及桁架布料系统,实现了全封闭式作业和混凝土运输及浇筑全过程的自动化。
该系统由一台HZS180搅拌机、鱼雷罐、鱼雷罐环形闭合轨道、布料机、布料机桁架运行轨道等几部分组成。搅拌机将搅拌好的混凝土注入鱼雷罐中,鱼雷罐通过环形轨道,运行至预制构件浇筑区,布料机通过遥控操作运行至鱼雷罐下方进行接料,布料机通过运行轨道将混凝土运送至液压模板上方,进行预制构件混凝土的均匀布料,放料完的鱼雷罐沿环形闭合轨道回转至搅拌机接料口,形成一个循环的接料与放料过程。(如图3所示)
该系统具有以下几个创新点:
(1)搅拌机加高改造
为配合环形闭合鱼雷罐运输轨道,解决传统鱼雷罐从搅拌站出料口至布料机处轨道坡度较大、运输速度较慢等问题,本系统充分考虑液压模板高度、工作空间、布料机高度、鱼雷罐高度等因素,对搅拌机采用定制化加高设计,出料口高度为8.48米,比常规搅拌机加高了4.28米。(如图4所示)
(2)将传统鱼雷罐单通道改为环形闭合通道
区别于现有的单通道鱼雷罐运输轨道和混凝土罐车,预制构件环形自动化生产线采用环形的鱼雷罐运输系统代替,进一步提高预制构件生产中混凝土浇筑工艺的自动化程度。
不同于传统单通道鱼雷罐运输轨道一次只能用一个鱼雷罐运输混凝土,鱼雷罐环形运输轨道可同时悬挂多个鱼雷罐进行接料和放料,满足多条生产线同时进行预制构件浇筑,在提高施工效率的同时,实现大批量、工期短的预制构件快速制造。(如图5所示)
(3)布料机液压伸缩装置
为解决布料机桁架与作业工人相互干扰的问题,每台布料机上配备了4个80厘米长的液压升降杆,最大伸缩量为60厘米,实现混凝土浇筑时布料斗能下放到离构件顶面30厘米距离内,可有效避免因布料高度过大引发的混凝土离析问题。空载时能提升布料斗,从而解决运输过程需要工人避让等安全问题。(如图6所示)
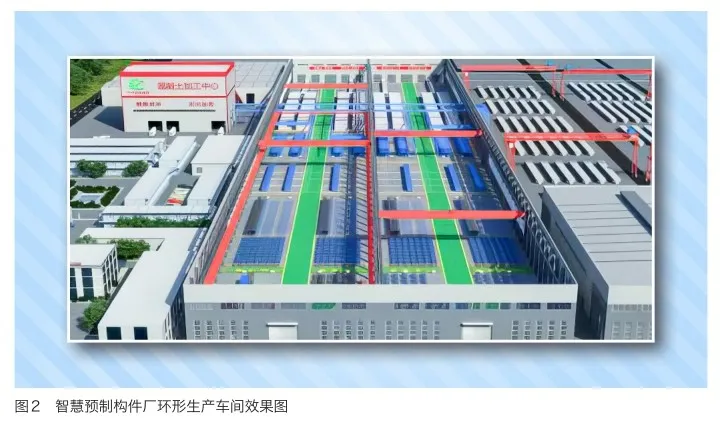
通过混凝土环形运输系统及桁架布料系统,可实现预制构件混凝土自动化运输及浇筑,混凝土运输及布料用工需求可减少75%;使用电力替代柴油驱动,不仅可降低成本58%,还减少对环境的污染,具有良好的经济效益和社会效益。另外,这套系统可有效降低作业人员工作强度,避免厂区混凝土运输车与作业人员的相互干扰,保证安全生产。系统获第三届全国公路微创新大赛金奖。
2.智能控温蒸养箱
构件脱模后移动至蒸汽养生区。蒸汽养生区由两个相邻智能控温蒸养箱组成,可同时满足两榀构件的蒸汽养生需求。智能控温蒸养箱由蒸养箱、变温蒸养设备和智能控温系统组成,蒸养箱采用试验恒温养护室标准建设,外包隔热保温层。智能控温蒸养系统可根据预设的蒸养制度自动调整升降温速度、恒温时间、空气湿度等,提升混凝土早期强度及弹性模量增长速度,节省张拉前养生时间。(如图7所示)
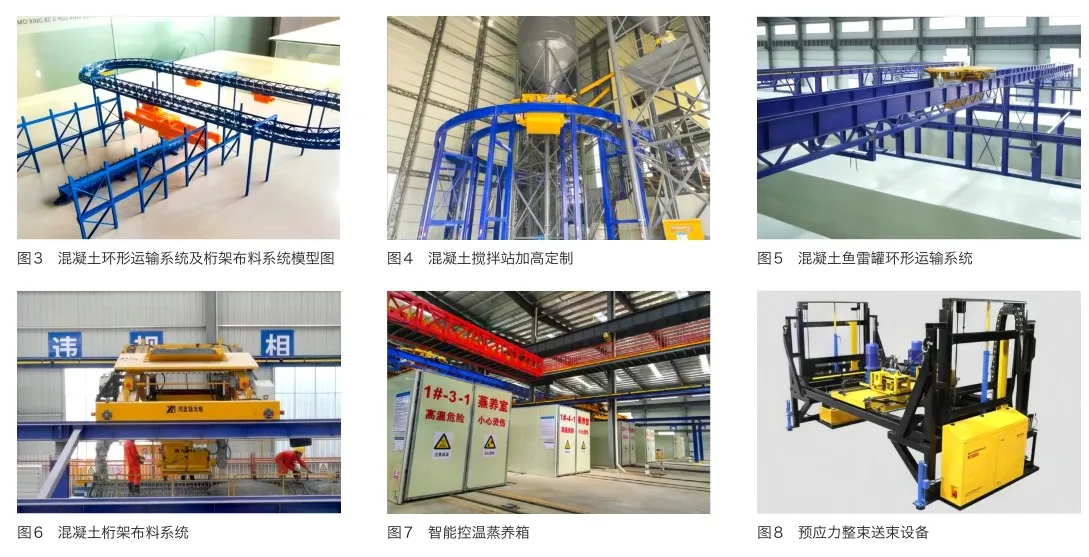
3.预应力整束送束设备
为解决预制构件预应力离散问题,引进应用卡瓦式钢绞线整束送束机,该机械可模拟人手握裹钢绞线,通过PLC控制实现自动穿束,极大地提高了整体穿束效率。(如图8所示)
4.自行式台车自动打磨清理设备
智慧预制构件厂引进了自行式台车自动清理机,将其安装在环形生产线回转通道上,自行式台车在回程途中即可完成自动打磨清理。(如图9所示)
5.自行式台车附着式振捣设备
插入式振捣器难以触及预制构件底板,导致底板混凝土振捣效果差。通过在自行式台车底模下加装附着式振捣器,解决了预制构件底板混凝土振捣不密实等问题。(如图10所示)
(三)创新工艺技术研发
1.绿色环保施工技术
首先,地基处理大面积采用生态减沉桩,可减小对土地的伤害。科研成果《块石垫层+竹桩复合地基减沉关键技术及施工技术》,通过绿色环保的竹桩和易取得的块石,解决了南沙软土地区地基加固的难题,施工成本相对管桩每亩可节省约6万元,具有良好的经济效益,荣获第二届全国公路微创新大赛银奖。(如图11所示)
其次,采用清洁能源天然气进行蒸汽养生,实现了最大限度的绿色环保。
2.环形生产线施工工艺技术
当前,传统预制构件生产工艺存在生产效率低、占地面积大、制造周期长、台座利用率低、产品质量不可控、受环境影响大等问题。为了有效保证产品质量、加快生产进度、节约临时用地,智慧预制构件厂开创性地引入与改进预制构件环形生产线施工工艺技术。
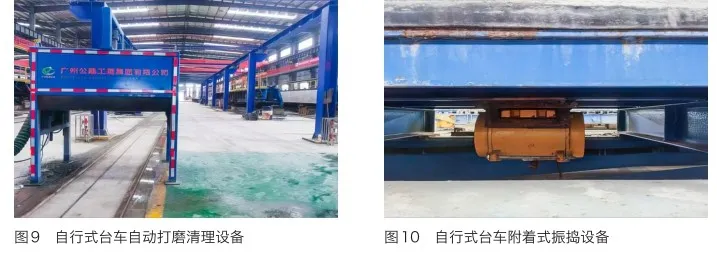
环形生产线施工工艺流程为定位胎具钢筋绑扎→自行式台车就位→自行式台车纵移至浇筑区→安装液压侧模→吊装钢筋及安装箱形构件内模→安装顶板钢筋→混凝土运输(鱼雷罐)→混凝土浇筑(布料机)→自行式台车纵移至智能控温蒸养箱养生→自行式台车带构件纵移至张拉区张拉→横移摆渡车带构件横移至存放区→提构件门吊提构件至存放区存放→横移摆渡车带自行式台车横移至专用回转通道,各道工序通过自行式台车紧密串联形成闭合环线。(如图12所示)
环形生产线施工工艺的应用使得生产效能显著提升,每条生产线预期产能可达每天1片;台座周转效率大大提高,整体节约用地约30%。
3.养生用水循环处理技术
传统预制构件厂对于预制构件的养护用水均为一次性用水,不仅造成了水资源的浪费,而且排放的养护用水也会对环境造成一定污染。处理方法为在养护用水蓄水池中进行絮凝沉淀处理,将污水中的胶体和细微悬浮物凝聚成絮凝体使其沉淀。该处理方法不但可以去除污水中的粒径为10- 6到10- 3毫米的细小悬浮颗粒,而且还能够去除色度、油分、微生物、氮和磷等富营养物质、重金属以及有机物等,经水质检测机构监测后该级处理的水样已达到最新版《公路桥涵施工技术规范》JTG/T3650- 2020对预制构件养护用水的标准,可再次应用于构件养护。
4.智能控温蒸汽养生技术
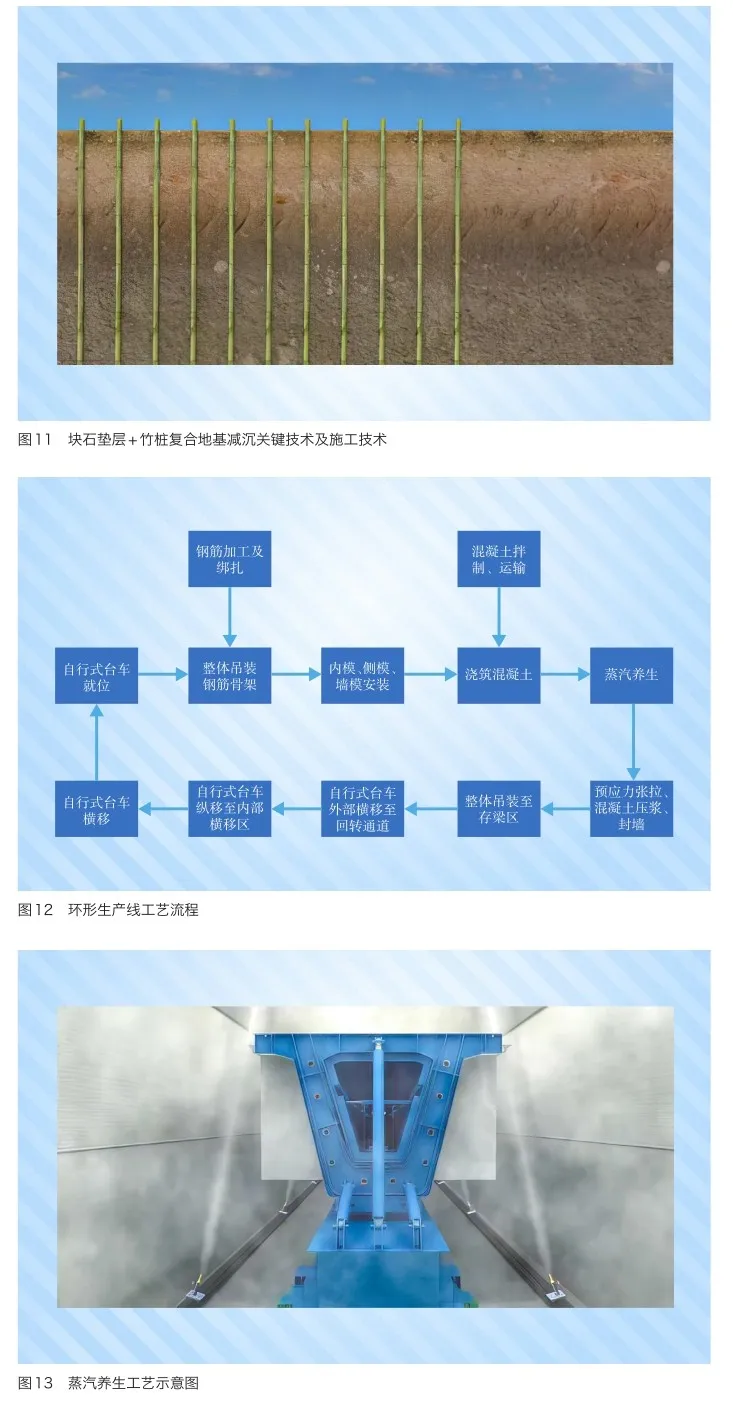
目前,环形生产线施工工艺在预制构件施工中应用越来越广泛。通过自行式台车的循环流转,各道工序施工效率均得到了显著提升。但是,制约环形生产线流水生产的关键工序是养生,传统养生方式为覆盖洒水养生,养生时间不少于5天,且强度和弹性模量不低于设计强度和弹性模量的80%时,方可进行张拉压浆作业。洒水养生不仅工作效率低,而且对预制构件外观质量影响较大,在桥梁预制构件工业化生产过程中已不再适用。
针对这一问题,智慧预制构件厂以实际需求为出发点,引入蒸汽养生工艺,并根据混凝土配合比情况试验并研究出一套满足环形生产线流水生产的蒸汽养生工艺技术,采用50摄氏度高温蒸养,并严格控制其升温、降温速率及恒温时间,将总体养生时间控制在36~48小时内,确保每条环形生产线每天可流水生产1榀预制构件,大幅提高养生效率,混凝土后期收缩小,构件外观质量显著提升,具有较好的经济效益及社会效益。(如图13所示)
(四)数字化构件厂管理平台
智慧预制构件厂按照智能化、数字化要求,引入并改进了“环形生产线”,同时建立了基于BIM技术和数据驱动的智慧管理系统,实现了预制构件生产智能化及全过程数字化管理。
针对预制构件生产管理,智慧预制构件厂开发的基于BIM技术的智慧管理平台,包含物联网设备对接、UE4大屏展示、MES系统、ERP系统、KM系统、BIM数据库、生产计划、质量安全、材料管理系统等模块,将生产管理全面信息化、数字化,可实现预制构件生产排产、钢筋余料优化、生产过程信息自动记录、构件存放位置算法推荐和可视化构件寻找等一站式管理。同时,针对预制构件生产,开发定制微信小程序,配合贴在预制构件上的二维码,可实现预制构件工序全面信息化,同时可完成构件存放数字化、构件寻找便捷化。
四、实施成效
(一)经济效益
1.相较于传统生产线工艺,采用环形生产线可节约22%的人工投入(测算节约成本800万元),真正实现了以机械化换人、以自动化减人的目的。
2.移动台座的使用,提高了台座周转效率,节省了约30%的施工占地,节约成本450万元。
3.针对软土地基开发的生态减沉技术,其施工成本相对管桩每亩可节省约6万元,预估节约成本2100万元。
4.蒸汽养生工艺的应用,使张拉前养生时间从传统的5天缩短至2天,生产效率提高了150%;蒸汽养生工艺的使用,提高了施工效率和施工质量,降低了整体施工成本。
5.标准化胎架、整体液压模板的使用,有效提高了预制构件的品质。
6.建设区域服务型智慧预制构件厂,可充分发挥其对周边项目的服务辐射能力,减少临时预制构件厂的重复建设,节约临建投入约5000万元。
(二)社会效益
1.节约用地:由于该工艺生产效能显著提升,提高了台座周转效率,整体节约用地约30%。
2.绿色低碳:利用清洁能源天然气进行蒸汽养生,可避免普通锅炉产生的粉尘污染,助力绿色可持续发展。
(三)业内评价
自区域服务型智慧桥梁预制构件厂建成以来,受到了上级领导及同行的广泛关注和学习。
2021年11月29日,在广东省交通运输厅组织召开的全省公路水运工程质量安全现场会上,智慧预制构件厂作为其中一处观摩点,现场展示了智慧建造、科技创新、科技强安、绿色环保等方面的亮点与典型做法,并获得了各级领导及同仁的一致好评。
2023年4月19日,国家交通运输部部长带队莅临智慧桥梁预制构件厂指导,并给予了高度评价。
五、下步思考
(一)建设预制构件自适应生产线
目前,环形生产线能生产的预制构件基本为标准构件,构件首尾端及端横梁基本固定,变化幅度受限,无法适应梁型变化。建设预制构件自适应生产线,把梁端及端横梁模板改造成液压可调节的方式,将是下一步智慧预制构件厂持续提升的方向。
(二)增加设备及硬件设施的物联监测
随着智慧桥梁预制构件厂运营时间的增加,厂房内的大型设备可能会出现故障,下一步将重点增加设备及硬件设施的物联监测,及时消除设备故障和安全隐患,确保作业安全。
编辑/车玉龙 统筹/苏晓