滚压收口工艺在中口径弹药的可行性应用
2024-12-06段东海
【摘要】作者在CA6140机床上开展了某中口径弹药滚压收口工艺试制,制定了试制工艺方案,并以该中口径弹药为例,进行了工艺验证,找出了影响弹药拉脱力的相关因素和控制措施,证明该弹药弹丸和药筒采用滚压收口连接的方法可行,且可满足批量生产需要,对同类型或更大口径的弹药采用滚压收口工艺有参考和借鉴价值。
【关键词】加工技术|滚压收口工艺|可行性研究|拉脱力
滚压工艺是指通过滚压刀具施加一定的压力,迫使药筒在与弹丸连接处整周产生塑形变形而嵌入弹丸预制环形槽中,将二者连接成一个可靠的整体的一种加工技术,多用于炮弹的风帽与弹体、弹带与弹体之间的连接[1]。收口工艺是指通过滚轮连续滚动施压或模具施压的方式改变金属管材口部的形状,将其他部件包覆连接起来的一种加工技术。
两种工艺的最大特点是成型压力小、方便快捷,在较小的设备上完成较大工件的连接[2],多应用于小口径弹药的生产,在中大口径弹药上应用较少,为验证两种工艺在中口径弹药弹丸与药筒连接的可行性和便捷性,作者在国内某中口径弹药研制过程中,开展了滚压收口工艺的可行性应用研究。
一、产品结构及要求
与国内小口径弹药的药筒多采用塑性较好的铜制或钢制件不同,该型弹药为降低成本、减轻弹重,药筒选用国内较为常见的铝材(牌号为2A12-T4)。药筒为薄壁筒形结构,与弹丸连接处厚度约1mm,在弹丸与药筒结合处设计了锥台的收口连接处和弧形凹槽的滚压连接处,其中收口处锥度约20°、长度5mm;滚压处为R4圆弧,圆弧深度为0.5mm。弹丸和药筒滚压收口后,要求连接牢固、可靠、无晃动,全弹同轴度不大于1.5mm,且连接后弹丸与药筒的拉脱力约15000N左右。
二、滚压收口工艺可行性分析
该型弹药整体结构为回转体,作者采用了国内应用比较广泛的CA6140车床平台进行可行性研究。滚压收口时,用车床卡爪夹紧弹丸,药筒口部套入弹丸,尾部套入专用尾顶(如图1所示),顶紧药筒后,启动机床,滚压刀具和收口刀具与药筒接触时,被摩擦力带动旋转,此时通过调整滚压刀具和收口刀具的进给量,使药筒在收口处和滚压处产生局部变形,当变形不断累积在弹丸底部凹槽内时,可将弹丸和药筒连接起来,初步分析,滚压收口工艺用于该型弹药弹丸和药筒连接的方案可行。
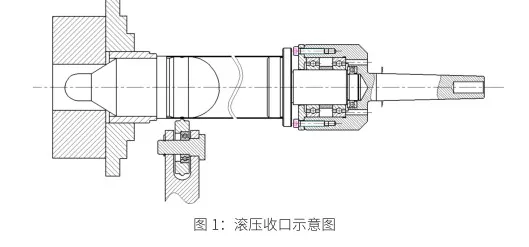
三、工艺方案
通过对弹药作用原理分析,为满足弹丸与药筒拉脱力基本一致的要求,作者初步判定滚压凹槽深度、收口锥度长度、连接处是否涂胶和药筒不同表面状况等因素均对拉脱力产生影响,故本次工艺研究拟采用模拟弹丸和药筒,从单个因素到综合因素等方面进行工艺试验,用万能拉力试验机测试二者拉脱力。
四、工艺试验
选定的CA6140车床转速范围为10~1400r/min,试验发现滚压时机床转速超过200r/min时,滚压刀具与药筒存在明显剪切现象,药筒减薄率较大,药筒内部变形小,连接不可靠;转速过低时,滚压力大且效率低,本次工艺研究机床转速均采用40r/min。
(一)单因素拉脱力试验
确定上述试验参数后,选定6发模拟弹丸进行了收口,其中3发涂环氧树脂胶,收口完成后自然固化24h。另选定3发进行滚压,测试弹丸和药筒拉脱力,数值见表1。
通过分析表1数据发现,滚压处比收口处对拉脱力影响更大,是否涂抹环氧树脂胶对拉脱力影响较小,但为满足该弹药密封性要求,后续试验均采用涂胶方式,通过调整滚压深度的大小,测试滚压深度对拉脱力的影响。
(二)不同滚压深度拉脱力试验
作者进行了0.6mm、0.8mm和1.0mm三种深度的测试,每种深度各3发,收口深度采用1.8mm,涂胶,固化24h,分别测试其拉脱力,见表2。
试验发现,采用滚压深度0.8mm和1.0mm时的拉脱力均能满足设计要求,但三种状态下的全弹同轴度尺寸均出现超差现象。按1.0mm深度再次收口1发,固化24h后,直接解剖,发现滚压处药筒内部圆弧与弹丸凹槽存在明显未贴合现象。清洗胶层后,测量药筒滚压处壁厚,较未滚压处减少0.1mm左右。
作者分析认为,滚压时药筒壁厚存在减薄现象,造成药筒与弹丸不贴合现象。为保证全弹同轴度,确保滚压处药筒内部圆弧与弹丸凹槽贴合,需增加滚压深度或减小弹丸凹槽深度。
针对上述影响因素,作者将凹槽深度调整为0.3mm,滚压收口3发,其拉脱力分别为11611N、10257N和12208N,平均拉脱力为11359N。另将3发凹槽不变,滚压进给量增加到1.2mm,其拉脱力分别为15357N、15608N和15055N,平均拉脱力为15340N。
试验发现,滚压凹槽深度0.3mm时,其拉脱力明显变小,不满足设计要求。当滚压进给量增加到1.2mm时,弹丸和药筒连接无晃动,且拉脱力与采用1.0mm和0.8mm时基本一致。
(三)表面处理后拉脱力试验
所有弹药产品均有寿命要求,弹丸和药筒需做好防腐。常见的铝合金表面处理方法有阳极氧化、化学转化、电镀和微弧氧化等[3]。军工行业铝合金制品多采用阳极氧化工艺技术,其应用范围广,技术成熟且成本较低。但铝合金在氧化后,其表面会形成一层结构致密、硬度较高的氧化膜,该氧化膜会提升铝合金表面的摩擦系数和耐磨性,可能对拉脱力有影响。
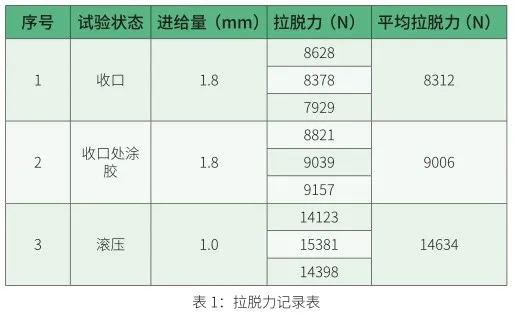
为验证氧化膜层对拉脱力的影响,作者在相同滚压收口参数下,分别测试了弹丸和不同表面状态下药筒的拉脱力,每种状态测试3发,拉脱力记录见表3。
试验发现,相同滚压收口参数下,氧化后弹丸与无氧化药筒的拉脱力与均未氧化的状态基本一致,氧化后的弹丸与中间处理药筒拉脱力稍有增大,二者均氧化的拉脱力显著变大。试验证明,表面处理确实对弹丸和药筒的拉脱力有影响,氧化膜层的硬度和致密性会显著增大拉脱力。
(四)试验数据分析
通过上述试验,作者确定了无表面处理下的弹丸和药筒,在选择滚压深度为0.5mm、滚压进给量1.2mm及收口进给量1.8mm参数时,二者拉脱力和全弹同轴度均可满足设计要求。但药筒和弹丸均进行氧化或中间处理后,相同参数下,拉脱力明显增加,为满足设计要求,可调整滚压凹槽深度和滚压进给量等相关参数。
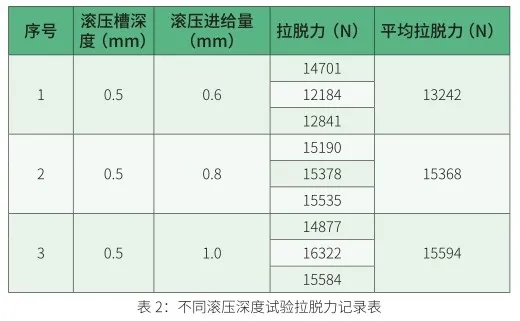
五、结语
传统的中大口径弹药战斗部与火箭部、弹丸与药筒等多采用螺纹结构连接,作者通过对某中口径弹药的结构分析,设计了滚压收口刀具和夹具,并通过工艺试验确定了相关参数,在多种组合的条件下,开展了不同状态下弹丸和药筒的拉脱力试验及分析,找出了影响拉脱力的相关因素,表明滚压收口工艺在中大口径弹药的生产中可行,也给中大口径弹药设计提供了一种新的可行方案。中国军转民

参考文献
[1]查宏振,刘载杰,陈惠武,等.炮弹与火箭弹制造工艺学[M].北京:国防工业出版社,1982:178-179.
[2]孙大涌,屈贤明,张送滨.先进制造技术[M].北京:机械工业出版社,2002:339-340.
[3]刘海萍,邹忠利,毕四富.铝合金、镁合金表面强化技术[M].北京:化学工业出版社,2019:11-12.
(作者简介:段东海,福建兵工装备有限公司、福建省弹药工程与枪械研究重点实验室,中级工程师,本科,研究方向为机械加工工艺)